Welcome to our comprehensive guide on understanding the concrete thickness required for car parks in Auckland. In this article, we will delve into the significance of concrete thickness, explore the local standards and regulations, and discuss the factors that influence the required thickness for car parks. Auckland’s unique climate and traffic conditions make it essential to get the concrete thickness right to ensure durability and safety. Whether you’re a homeowner planning a residential car park or a business owner looking to construct a commercial parking space, this guide will provide you with valuable insights and practical tips to ensure your car park stands the test of time.
The standard concrete thickness for car parks in Auckland typically ranges from 100mm to 150mm, depending on factors such as traffic load, subgrade quality, and intended use. Residential car parks often require around 100mm, while commercial car parks designed for heavier vehicles may need up to 150mm to ensure durability and safety.
- Understanding Concrete Thickness
- Concrete Thickness Standards In Auckland
- Factors Influencing Concrete Thickness
- Construction Best Practices
- Case Studies And Examples
- FAQs: About How Thick Is The Concrete In A Car Park In Auckland
- What is the standard concrete thickness for car parks in Auckland?
- Why is concrete thickness important for car parks?
- How does traffic load affect concrete thickness in car parks?
- What role does subgrade quality play in determining concrete thickness?
- How do Auckland's climate conditions impact concrete thickness?
- Can concrete thickness be adjusted after construction?
- What are the signs of insufficient concrete thickness in a car park?
- How can reinforcement enhance the durability of concrete in car parks?
- What are the best practices for maintaining a concrete car park?
- Where can I find local regulations for car park construction in Auckland?
- Conclusion
Understanding Concrete Thickness
Definition
Concrete thickness refers to the depth or width of a concrete slab. In the context of car parks, this measurement is critical as it directly impacts the durability and functionality of the parking area. Proper concrete thickness ensures that the surface can withstand the weight of vehicles and the stress from constant use. Without adequate thickness, car parks are prone to cracking, which can lead to expensive repairs and safety hazards.
Standard Measurements
Globally, the standard measurements for concrete thickness in car parks can vary based on usage and local building codes. Typically, for light-duty car parks, that accommodate passenger vehicles, a concrete thickness of 100-150 mm (4-6 inches) is recommended. For medium to heavy-duty car parks that handle larger vehicles, such as delivery trucks or buses, the thickness can range from 150-200 mm (6-8 inches). These standards are essential to ensure that the concrete can support the expected loads and provide a long-lasting surface.
Importance
The importance of the right concrete thickness in car parks cannot be overstated. Here are a few key reasons:
1. Longevity: Proper thickness ensures the concrete can withstand the wear and tear of daily use, extending the lifespan of the car park. Thinner concrete may deteriorate quickly under heavy traffic, leading to frequent maintenance and repairs.
2. Vehicle Support: Adequate thickness provides the necessary support for vehicles of various sizes. It prevents the surface from cracking or breaking under the weight, which is crucial for safety and functionality.
3. Load Distribution: Thicker concrete helps in better load distribution, reducing the stress on the underlying ground. This is particularly important in areas with poor soil conditions or high traffic volumes.
4. Cost-Effectiveness: While thicker concrete might seem more expensive initially, it reduces long-term costs by minimizing the need for repairs and maintenance. Investing in the right thickness from the start can save significant money over time.
In summary, understanding and implementing the correct concrete thickness for car parks is a vital aspect of construction that impacts the safety, durability, and overall performance of the parking area. By adhering to standard measurements and recognizing the importance of this factor, you can ensure that your car park remains functional and safe for years to come.
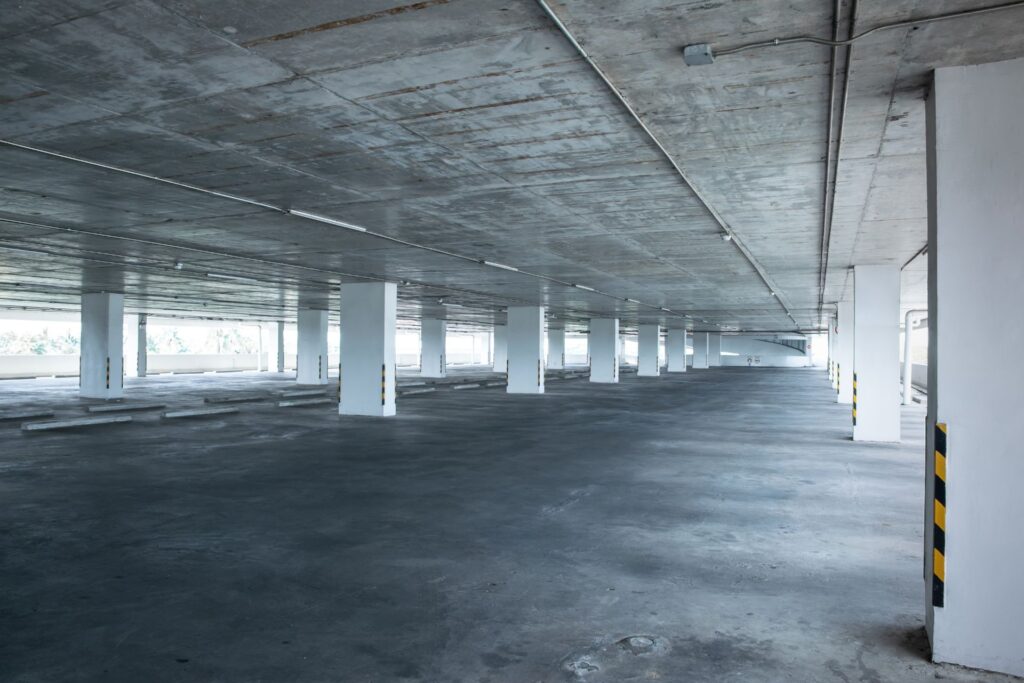
Concrete Thickness Standards In Auckland
Local Regulations
When constructing car parks in Auckland, it is crucial to adhere to the local building codes and regulations set forth by the Auckland Council. These regulations ensure the safety, durability, and longevity of the structures. The Auckland Council provides specific guidelines on the required concrete thickness for various types of car parks, considering factors such as soil conditions, load-bearing requirements, and environmental impact. Compliance with these regulations is mandatory for obtaining the necessary permits and avoiding potential fines or reconstruction costs.
The Building Code of New Zealand (NZBC) and the New Zealand Standard (NZS) are primary references for construction standards, including those for car parks. These standards outline the minimum requirements for materials, construction methods, and structural integrity. For instance, the NZS 3101 (Concrete Structures Standard) and NZS 3109 (Concrete Construction) provide detailed specifications for concrete thickness, reinforcing materials, and other critical factors.
Typical Thickness
In Auckland, the typical concrete thickness for car parks varies depending on whether the car park is for residential or commercial use.
Residential Car Parks: For residential car parks, the concrete slab thickness generally ranges from 100mm to 150mm. This thickness is sufficient to support the weight of standard vehicles typically found in residential settings. Additionally, residential car parks may have less frequent traffic, reducing the need for thicker slabs.
Commercial Car Parks: Commercial car parks, on the other hand, require a more robust construction due to the higher volume of traffic and the presence of heavier vehicles, such as delivery trucks and service vehicles. The standard thickness for commercial car park slabs in Auckland is typically between 150mm to 200mm. In some cases, especially in areas with poor soil conditions or heavy usage, the thickness may exceed 200mm to ensure adequate support and longevity.
Comparisons
When comparing Auckland’s concrete thickness standards for car parks to those in other regions or countries, several differences and similarities can be observed.
Australia: In neighboring Australia, concrete thickness standards for car parks are quite similar to those in Auckland. For instance, residential car parks usually have a slab thickness of 100mm to 150mm, while commercial car parks range from 150mm to 200mm. Both countries follow stringent building codes and standards to ensure structural integrity and safety.
United States: In the United States, the standards can vary significantly depending on the state and local regulations. However, the general trend is comparable, with residential car park slabs typically being around 100mm to 150mm thick and commercial slabs ranging from 150mm to 250mm. The American Concrete Institute (ACI) provides detailed guidelines on concrete thickness, similar to New Zealand’s NZS standards.
Europe: European countries also exhibit variations in concrete thickness standards based on local regulations. For example, in the UK, residential car parks often have a minimum thickness of 100mm, while commercial car parks require slabs of at least 150mm to 200mm. The Eurocode 2 (Design of Concrete Structures) offers a comprehensive framework for concrete construction, paralleling the NZBC and NZS guidelines.
Overall, while there are regional differences in specific requirements and regulations, the fundamental principles of ensuring adequate thickness for load-bearing capacity and durability remain consistent across different regions. Auckland’s adherence to these principles, combined with its local regulations, ensures that car parks are constructed to high standards, providing safety and longevity for users.
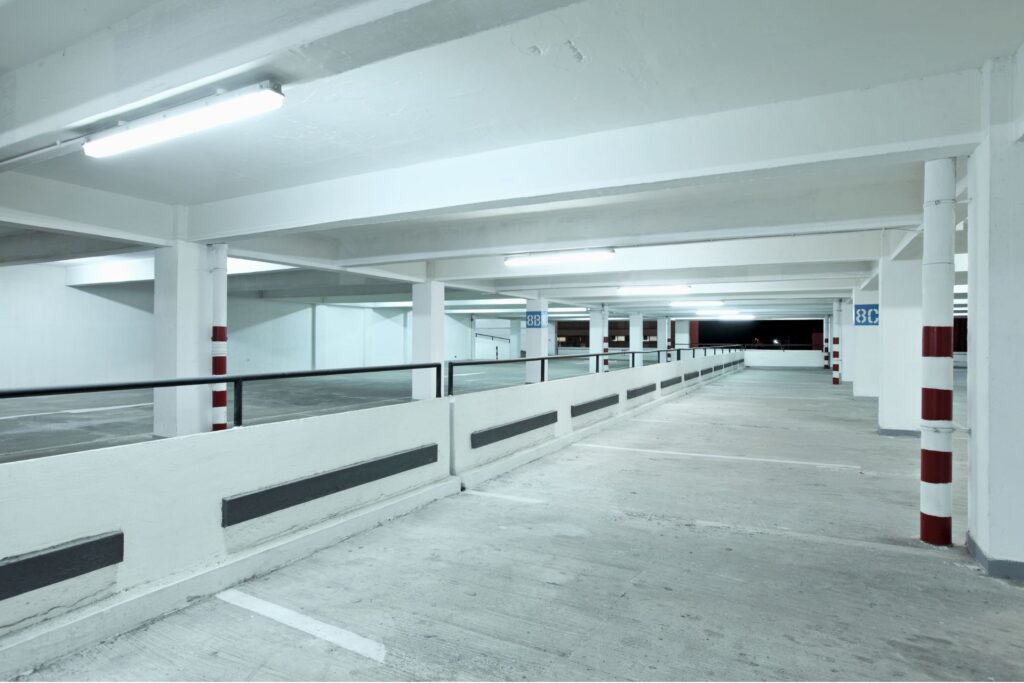
Factors Influencing Concrete Thickness
When determining the appropriate thickness for concrete surfaces, several crucial factors come into play. These elements ensure that the concrete performs well under various conditions and meets the demands of its intended use. Here, we explore the key factors that influence concrete thickness.
Traffic Load
The volume and weight of vehicles that will use the concrete surface are primary considerations. For instance, a driveway that primarily accommodates passenger cars will require a different thickness compared to one that handles heavy trucks.
Light Traffic: For areas with light traffic, such as residential driveways where only cars and small trucks are present, a concrete thickness of around 4 inches (10 cm) is typically sufficient.
Heavy Traffic: In contrast, surfaces that bear heavy loads, like commercial loading docks or industrial areas, need a significantly thicker slab. These might require concrete thicknesses of 6 to 8 inches (15-20 cm) to support the weight without cracking.
Mixed Use: Car parks that cater to both light and heavy vehicles must find a balance. Here, a thickness of around 5 to 6 inches (12 to 15 cm) is often recommended to handle varied stresses.
Subgrade Quality
The subgrade, or the soil beneath the concrete, plays a vital role in determining the necessary thickness. Good preparation and quality subgrade can enhance the durability of the concrete.
Poor Subgrade: If the underlying soil is weak or poorly compacted, it can shift or settle over time, leading to cracks in the concrete. In such cases, a thicker slab is necessary to distribute the load more evenly and reduce the risk of damage.
Well-Prepared Subgrade: On the other hand, a well-prepared and compacted subgrade provides a stable foundation, potentially allowing for a thinner slab while still maintaining strength and durability.
Climate Conditions
Auckland’s unique climate conditions, characterized by significant rainfall and temperature variations, also affect concrete thickness requirements.
Rainfall: High levels of rainfall can weaken the subgrade and cause it to shift, necessitating a thicker concrete slab to prevent cracking and maintain structural integrity.
Temperature Variations: Fluctuations in temperature can cause concrete to expand and contract. In regions like Auckland, where temperatures can vary, thicker slabs can help mitigate the effects of thermal expansion and contraction, reducing the risk of cracking.
Intended Use
The intended use of the concrete surface is another critical factor influencing its thickness. Different applications demand varying levels of strength and durability.
Light Vehicles: For areas intended only for light vehicles, such as residential driveways, a thinner concrete slab (4 inches) is usually adequate.
Heavy Vehicles: Surfaces designed to accommodate heavy vehicles, like commercial truck parking areas, require thicker slabs (6 to 8 inches) to withstand greater loads.
Mixed-Use Car Parks: Car parks that serve both light and heavy vehicles need a medium thickness (around 5 to 6 inches) to handle the diverse stresses without compromising performance.
Understanding these factors is essential for ensuring that the concrete surface not only meets current needs but also remains durable and functional over time. Proper consideration of traffic load, subgrade quality, climate conditions, and intended use will lead to a well-performing concrete structure suited to its environment and usage.
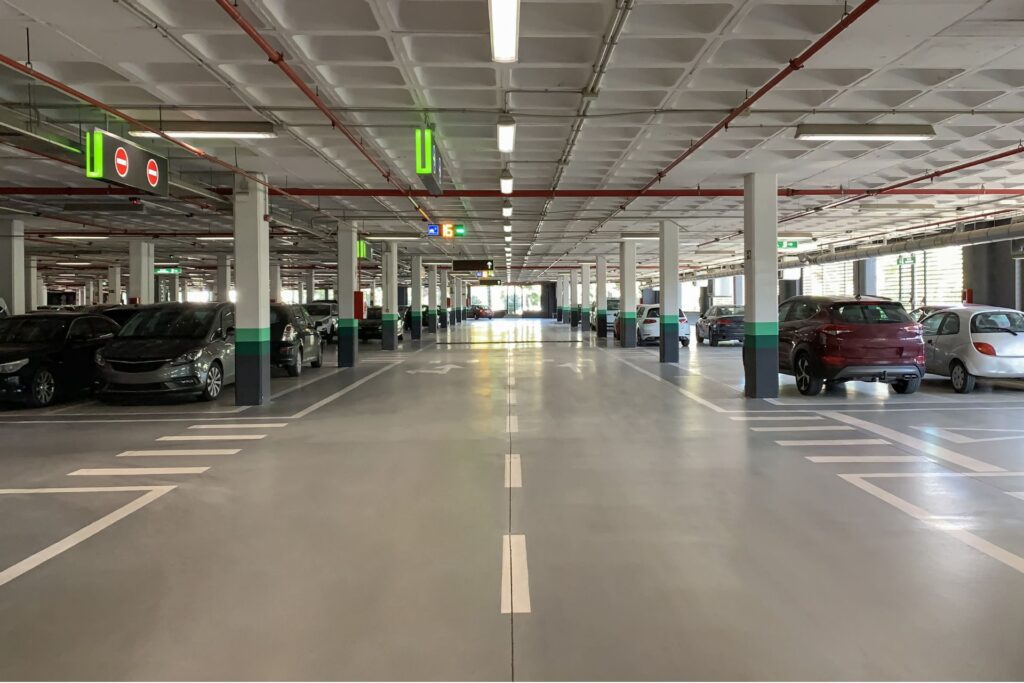
Construction Best Practices
Material Quality
When it comes to constructing durable and long-lasting concrete structures, the quality of materials used cannot be overstated. High-quality materials ensure that the final product will be resilient, sturdy, and capable of withstanding the test of time and environmental stressors. One crucial element is the mix design—the recipe for your concrete. A well-designed mix will include the right proportions of cement, aggregates (such as sand and gravel), water, and any necessary additives. This careful balance ensures that the concrete will have the desired workability, strength, and durability. Using subpar materials or incorrect mix proportions can lead to weak concrete that is prone to cracking, spalling, and other forms of deterioration.
Reinforcement
Reinforcement plays a pivotal role in enhancing the strength and structural integrity of concrete, particularly in areas subjected to heavy loads, such as car parks. Reinforcing materials like rebar (reinforcing bars) and mesh are embedded within the concrete to provide additional tensile strength. Concrete is naturally strong in compression but weak in tension; reinforcement helps bridge this gap. Rebar, typically made of steel, is placed in strategic positions within the concrete formwork before the concrete is poured. This reinforcement absorbs tensile forces, preventing the concrete from cracking under load. Mesh, another form of reinforcement, is often used in slabs and pavements to distribute loads evenly and reduce the risk of surface cracking.
Proper Curing
Curing is a critical process in concrete construction that significantly impacts the strength and durability of the final product. Proper curing involves maintaining adequate moisture, temperature, and time conditions to allow the concrete to hydrate and develop its full strength. The curing process typically starts immediately after the concrete is placed and continues for several days or weeks, depending on the specific requirements of the project. Effective curing can be achieved through various methods, such as water curing (keeping the surface wet), using curing compounds, or covering the concrete with wet burlap or plastic sheets. Proper curing ensures that the concrete achieves its intended strength, reduces the likelihood of surface cracking, and enhances its overall durability and resistance to wear.
Regular Maintenance
Maintaining car park concrete is essential to ensure its longevity and structural integrity. Regular maintenance helps prevent issues such as cracking, spalling, and general wear and tear. Here are some practical tips for maintaining concrete surfaces:
1. Cleaning: Regularly clean the surface to remove debris, dirt, and stains that can deteriorate the concrete over time.
2. Sealing: Apply a high-quality sealant to protect the concrete from moisture penetration, which can cause cracking and surface damage.
3. Repair Cracks Promptly: Address any cracks or damage immediately to prevent them from worsening. Small cracks can be repaired using concrete patching materials, while larger issues may require professional intervention.
4. Control Joint Maintenance: Ensure that control joints are in good condition. These joints help manage cracking by allowing the concrete to expand and contract without causing significant damage.
5. Avoid Deicing Chemicals: Minimize the use of harsh deicing chemicals, as they can cause concrete to deteriorate. Opt for safer alternatives or mechanical methods for snow and ice removal.
By following these best practices, you can ensure that your concrete car park remains in excellent condition, providing a safe and durable surface for vehicles and pedestrians alike. Proper material selection, reinforcement, curing, and maintenance are all integral components of a successful concrete construction project.
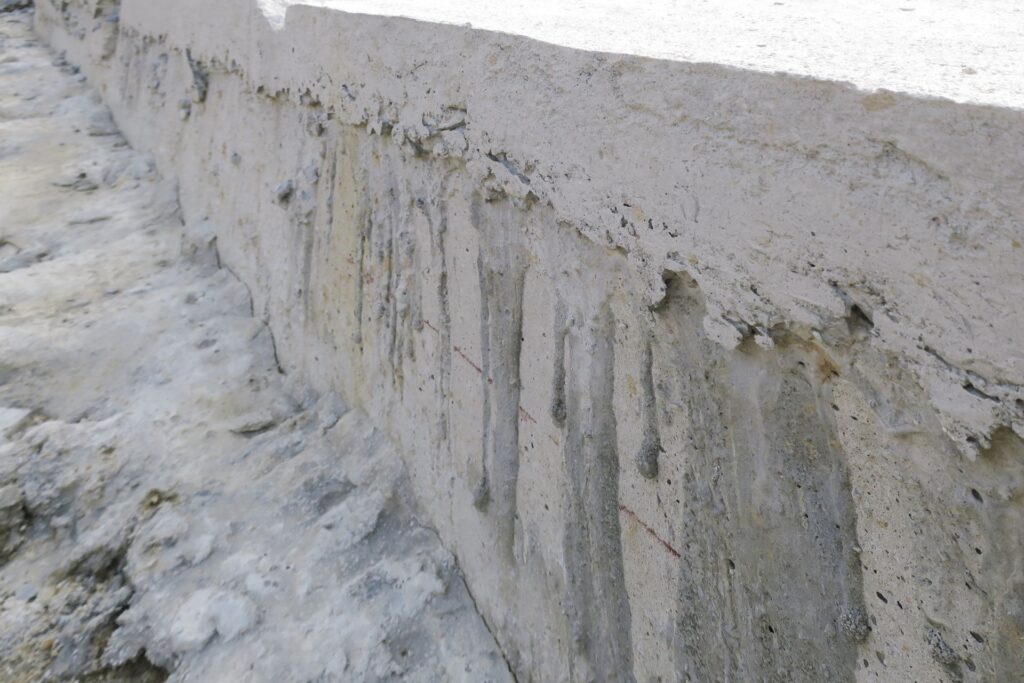
Case Studies And Examples
Local Examples
To illustrate the importance of proper concrete thickness in car parks, let’s look at some successful projects in Auckland. One prime example is the Britomart Car Park, known for its robust construction and durability. This car park features a concrete thickness of 250mm, which was chosen based on heavy traffic and the need for long-term resilience. The result is a car park that has withstood the test of time, providing a reliable parking solution for thousands of vehicles daily.
Another notable example is the Westfield Newmarket Car Park. Here, engineers opted for a concrete thickness of 300mm, factoring in the high volume of vehicles and the potential for heavy loads. This additional thickness has proven beneficial, ensuring the car park remains free from significant cracks and deterioration. These local examples demonstrate how careful planning and appropriate concrete thickness can lead to long-lasting and efficient car parks.
Lessons Learned
However, not all car parks have enjoyed such success. There are valuable lessons to be learned from those who have failed due to inadequate concrete thickness or poor construction practices. For instance, a car park in South Auckland suffered severe cracking within just a few years of completion. The primary issue was the insufficient concrete thickness of 150mm, which could not support the heavy traffic load, leading to rapid wear and tear.
In another case, a car park in the Auckland CBD experienced premature deterioration due to substandard construction practices. Despite having a concrete thickness of 200mm, improper curing techniques and poor-quality materials led to surface spalling and structural weaknesses. These examples underscore the importance of not only selecting the right concrete thickness but also ensuring high construction standards and quality materials.
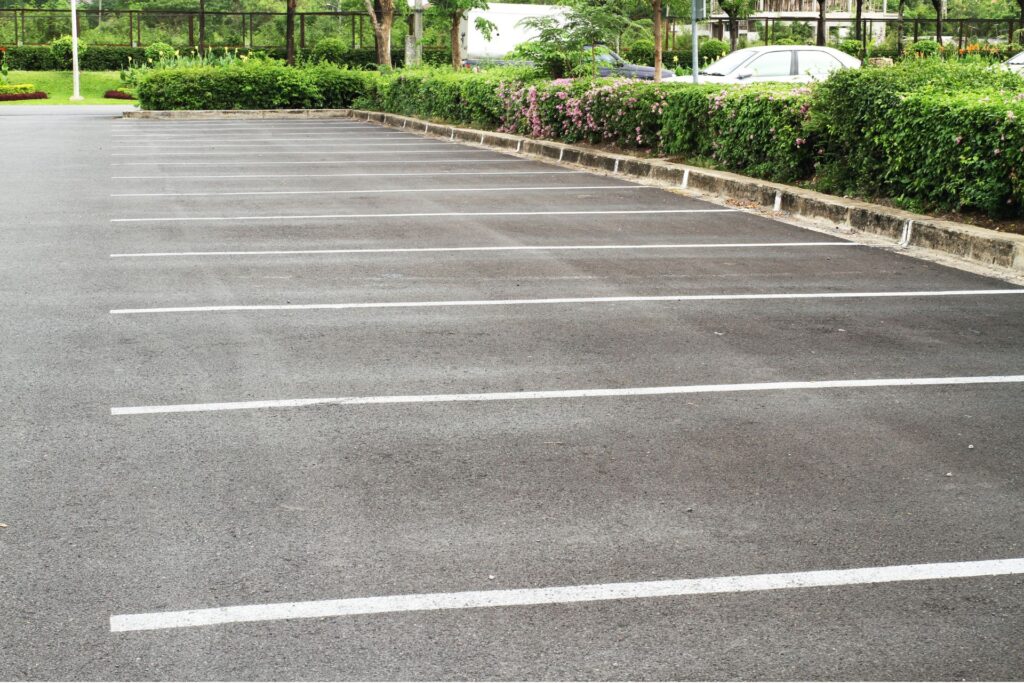
FAQs: About How Thick Is The Concrete In A Car Park In Auckland
What is the standard concrete thickness for car parks in Auckland?
The standard concrete thickness for car parks in Auckland typically ranges from 100mm to 150mm. Residential car parks usually require around 100mm, while commercial car parks designed for heavier vehicles may need up to 150mm.
Why is concrete thickness important for car parks?
Concrete thickness is crucial for ensuring the durability and safety of car parks. The right thickness helps support the weight of vehicles, prevents cracking, and extends the lifespan of the car park.
How does traffic load affect concrete thickness in car parks?
Traffic load significantly influences the required concrete thickness. Heavier traffic and larger vehicles necessitate thicker concrete to support the increased weight and prevent damage.
What role does subgrade quality play in determining concrete thickness?
The quality of the subgrade, or the soil beneath the concrete, affects the necessary thickness. A well-prepared subgrade with good compaction and stability allows for thinner concrete, while poor subgrade conditions may require thicker concrete for adequate support.
How do Auckland’s climate conditions impact concrete thickness?
Auckland’s climate, characterized by frequent rainfall and temperature fluctuations, can affect concrete. Proper thickness helps resist weather-related stresses, such as freeze-thaw cycles and moisture infiltration, ensuring the concrete remains durable.
Can concrete thickness be adjusted after construction?
Adjusting concrete thickness after construction is challenging and often not feasible. It is essential to plan and execute the correct thickness during the initial construction phase to avoid costly repairs or modifications later.
What are the signs of insufficient concrete thickness in a car park?
Signs of insufficient concrete thickness include cracking, uneven surfaces, sinking areas, and premature wear. These issues can compromise the safety and functionality of the car park.
How can reinforcement enhance the durability of concrete in car parks?
Reinforcement, such as rebar or mesh, improves the tensile strength of concrete, helping it withstand heavy loads and preventing cracks. Proper reinforcement is essential for maintaining the structural integrity of the car park.
What are the best practices for maintaining a concrete car park?
Regular maintenance includes cleaning, sealing cracks, addressing drainage issues, and applying protective coatings. Proper maintenance helps extend the lifespan of the concrete and prevents major damage.
Where can I find local regulations for car park construction in Auckland?
Local regulations for car park construction in Auckland can be found on the Auckland Council’s official website or by consulting with local building authorities. These regulations provide guidelines for concrete thickness, materials, and construction practices to ensure safety and compliance.
Conclusion
In conclusion, planning a car park involves several critical steps, from understanding local regulations and site analysis to choosing the right materials and ensuring proper drainage. Each of these elements plays a crucial role in creating a durable and efficient parking area. By consulting with experienced construction professionals, you can navigate these complexities and achieve the best results for your project. For those looking to dive deeper into the subject, we recommend exploring additional resources and articles on car park construction to gain a more comprehensive understanding.
About the Author:
Mike Veail is a recognized digital marketing expert with over 6 years of experience in helping tradespeople and small businesses thrive online. A former quantity surveyor, Mike combines deep industry knowledge with hands-on expertise in SEO and Google Ads. His marketing strategies are tailored to the specific needs of the trades sector, helping businesses increase visibility and generate more leads through proven, ethical methods.
Mike has successfully partnered with numerous companies, establishing a track record of delivering measurable results. His work has been featured across various platforms that showcase his expertise in lead generation and online marketing for the trades sector.
Learn more about Mike's experience and services at https://theleadguy.online or follow him on social media: