Achieving the right mix in concrete is key for any construction project’s success. This guide explains the best methods for mixing of concrete, essential tools, correct ratios, and common pitfalls.
Key Takeaways
- Proper concrete mixing is critical for achieving strength and durability in structures, as it ensures uniformity and prevents weaknesses that could lead to failure.
- Selecting the appropriate mixing method, whether hand mixing, machine mixing, or using ready mix concrete, is essential based on project size and specific needs.
- Maintaining the correct water-to-cement ratio is crucial for optimizing workability and strength in concrete; both excessive and insufficient water can adversely impact the final product.
Importance of Proper Concrete Mixing
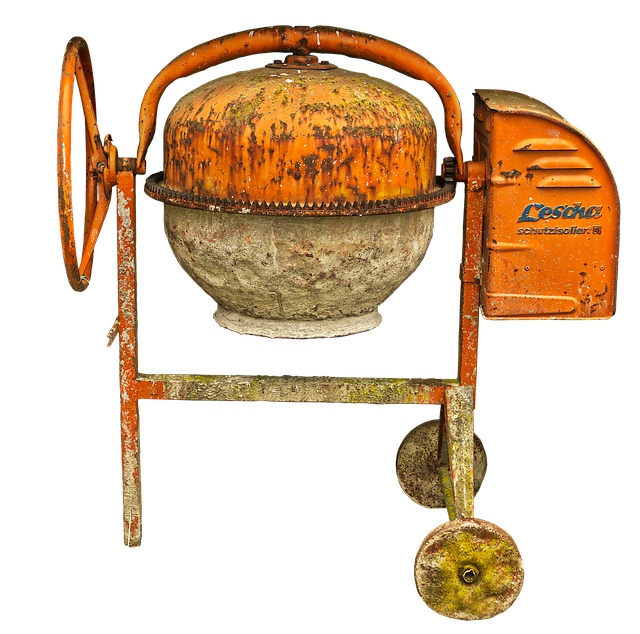
Achieving maximum strength and durability in concrete relies on proper mixing. The lifespan and structural integrity of any concrete structure depend on how well the materials are combined. Cement, the glue that holds the components of concrete together, requires careful handling to ensure it bonds effectively with sand and stones. This thorough mixing process is not just about blending ingredients; it’s about creating a uniform mixture that can withstand the test of time.
Achieving the desired consistency in concrete mixing demands extra care. Though it might seem daunting for beginners, proper guidelines simplify the process. Properly mixed concrete ensures a robust structure capable of lasting for generations. Imagine the satisfaction of knowing that the concrete you mixed today will stand strong for decades, providing safety and stability.
Proper concrete mixing is of paramount importance. It’s the foundation of good quality concrete that will support buildings, roads, and other structures. Mixing methods and techniques must ensure materials bond correctly, creating a homogeneous mixture that’s easy to place concrete and finish.
Without proper mixing, you risk weak spots, increased cracking, and ultimately, structural failure. Thus, mastering the art of mixing concrete is essential for any successful concrete project.
Different Methods for Mixing Concrete
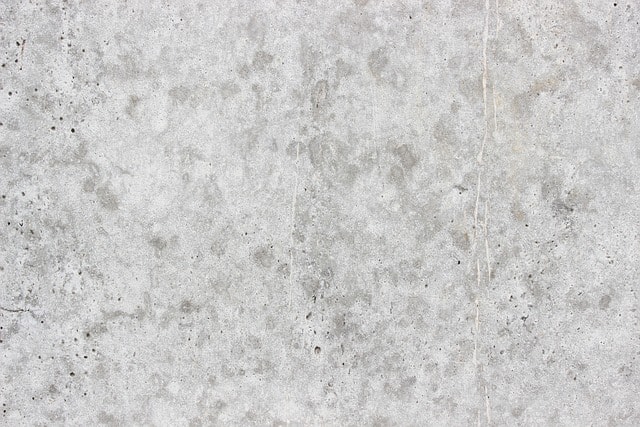
Choosing the right mixing technique determines the quality and characteristics of the concrete. There are various methods for mixing concrete, each suited to different scales and types of projects. Hand mixing suits smaller home projects, whereas machine mixing is ideal for larger endeavors. Additionally, ready mix concrete solutions offer a convenient and controlled option for many construction sites.
Hand mixing, which involves manually combining materials, suits small-scale projects but can lead to quality inconsistencies.
Conversely, machine mixing uses petrol, diesel, or electric mixers to achieve a uniform mix efficiently. For large-scale projects or areas with limited space, ready mix concrete is an excellent solution, as it is prepared at a concrete plant and delivered to the site. Each method has its advantages and is chosen based on the project’s specific needs and constraints.
Hand Mixing Techniques
Hand mixing refers to manually mixing the concrete materials. This method doesn’t use a mixer machine. This method is particularly handy for small home projects where the volume of concrete required is not very high. To ensure strength, it’s recommended to add 10% extra cement when using this technique. Typically, the process involves placing cement, sand, and stones on a flat surface, then using tools like shovels to mix them thoroughly.
Hand mixing can be effective for minor tasks but should never be used for crucial structural elements like columns or shear walls. Inconsistencies from manual mixing can lead to weak points, compromising the structural integrity.
The manual methods for placing concrete, such as using a wheelbarrow or power buggy, are sufficient for small projects but are not suitable for larger-scale applications where uniformity and strength are crucial.
Machine Mixing Techniques
Machine mixing uses a mixer to efficiently combine concrete materials. This method is particularly well-suited for larger projects, ensuring uniformity and quality in the concrete produced. Concrete mixers operate on petrol, diesel, or electricity, offering versatility for different project conditions. The use of a cement mixer significantly reduces mixing time, resulting in optimum consistency and uniformity.
Onsite central mix plants are ideal for large batches of concrete tailored to specific project needs. They produce large quantities of concrete, ensuring consistency and high quality.
Additionally, portable mixers can run on gasoline or electric power, providing the flexibility needed for different construction environments. Custom onsite mixing plants can also match the placement speed required for various jobs, enhancing workflow efficiency.
Ready Mix Concrete Solutions
Ready mix concrete reduces onsite mixing space, ideal for congested construction sites. It involves preparing concrete at a centralized plant and delivering it to the site, ensuring quality control and consistency. Ready mix trucks are suitable for larger applications, while portable mixers can handle smaller volumes effectively.
One of the significant advantages of ready mix concrete is its suitability for projects with limited space for mixing. However, timely delivery is crucial since delays can lead to issues like premature hardening of the mix.
Particularly useful in congested sites or road construction, ready mix concrete addresses space constraints that make onsite mixing challenging. This solution ensures that the concrete arrives well mixed and ready for immediate use, enhancing the efficiency and quality of the finished product.
Essential Tools for Concrete Mixing
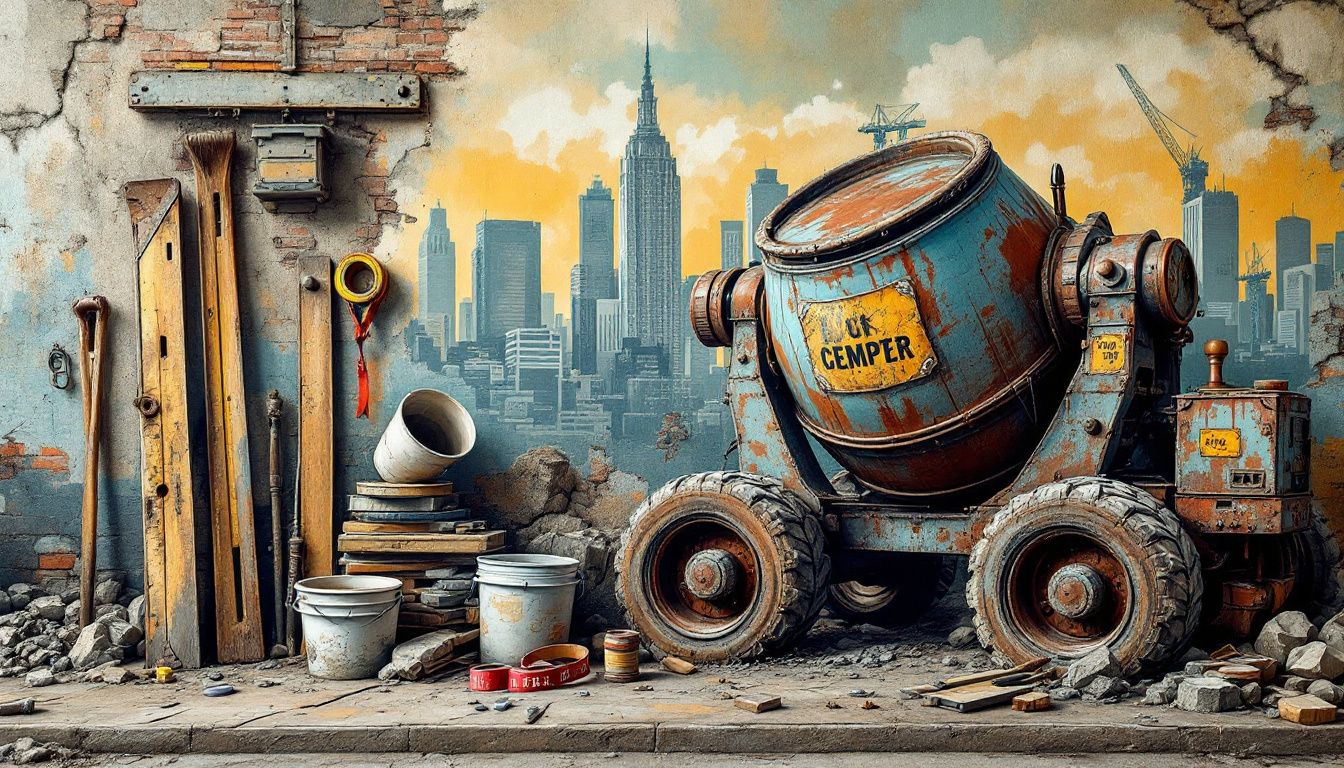
Effective concrete mixing requires the right tools. Here are some essential items:
- A sturdy mixing container, like a wheelbarrow or large bucket, is necessary for combining materials.
- Shovels and hoes are used for manual mixing.
- A mixing paddle attached to a drill can speed up the process.
- Safety gear like waterproof gloves, safety glasses, and dust masks protect against chemical exposure and dust.
By using the right tools and safety equipment, you can ensure a successful concrete mixing process.
Keeping a clean mixing area prevents concrete contamination. A wheelbarrow is useful for mixing concrete as it facilitates moving and dumping the mixed concrete. Using a masonry platform or flat sheet aids in uniformly combining materials during hand mixing.
Having all the necessary tools and a clean workspace ensures good quality concrete.
Understanding the Concrete Mix Ratio
The correct water-to-concrete mix ratio ensures strength and proper bonding of particles. Excess water reduces compressive strength and increases cracking risks. Too little water prevents particles from sticking together, compromising the mix’s integrity. The ideal mix ratio typically includes 60-75% aggregates, 7-15% cementitious materials, and 14-21% water.
Well-mixed concrete should be smooth and workable without being runny. Signs of a dry mix include mixing difficulty and lack of homogeneity.
Excess water causes bleeding, pooling on the surface and potentially leading to spalling. Maintaining the correct mix ratio is fundamental for quality concrete that meets project requirements.
Step-by-Step Guide to Mixing Concrete
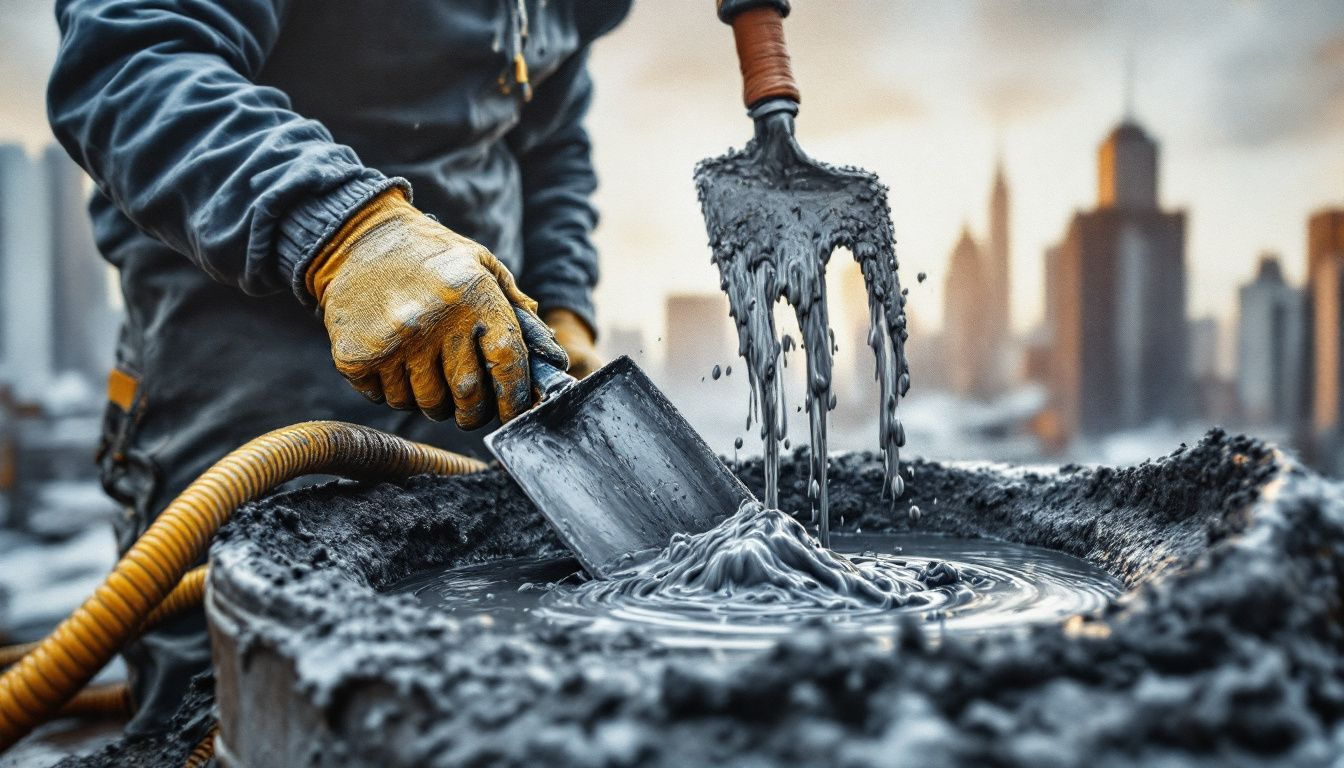
Proper concrete mixing is crucial for project success. The process involves gathering and preparing materials, adding water incrementally, and achieving the perfect mix consistency. Each step ensures the concrete is mixed thoroughly and uniformly before pouring.
The perfect mix should be consistent and workable without being too dry or runny. Thorough mixing ensures that all ingredients are combined before pouring.
Using tools like a sturdy wheelbarrow for transporting the mix and a mixing paddle attached to a drill can significantly speed up the process. These steps guide you toward the ideal consistency for your concrete project.
Preparing Materials and Equipment
Gathering gravel, sand, cement, and water is essential for a successful mix. Lay out all materials, ensuring readiness before mixing. This preparation step includes having the necessary equipment like a mixing container, shovel, and protective gear. Using flat iron sheet plates or a masonry platform for hand mixing helps achieve a uniform blend.
Proper preparation reduces effort during mixing and ensures the desired consistency. A clean and organized workspace prevents contamination and ensures proper bonding of mixed materials. Thorough preparation sets the stage for successful concrete mixing.
Adding Water to the Concrete Mix
Add water incrementally to control the mix’s consistency. Measure water into a bucket and add as needed. Add water slowly to avoid making the mix too wet. Closely monitor the water-to-cement ratio to maintain the concrete’s intended strength.
Adding water in small amounts better controls the mix’s consistency. If the mix appears too dry, gradually add more water until the desired consistency is achieved. If the mix becomes too wet, adjust by reducing the water content or adding more dry mix. Balancing water content is essential for quality concrete.
Achieving the Perfect Concrete Mix Consistency
The correct water-to-concrete mix ratio is crucial for achieving desired consistency and strength. Gradually add water to the dry concrete mix to prevent over-saturation and ensure consistency. Signs of a dry concrete mix include mixing difficulty and a rough texture; remedy by gradually adding small amounts of water.
A runny concrete mix often results from excess water; adjust by decreasing water content or adding dry mix. The perfect mix should be smooth and workable, ensuring maximum strength and durability when cured. This balance is crucial for your project’s success.
Common Issues in Concrete Mixing
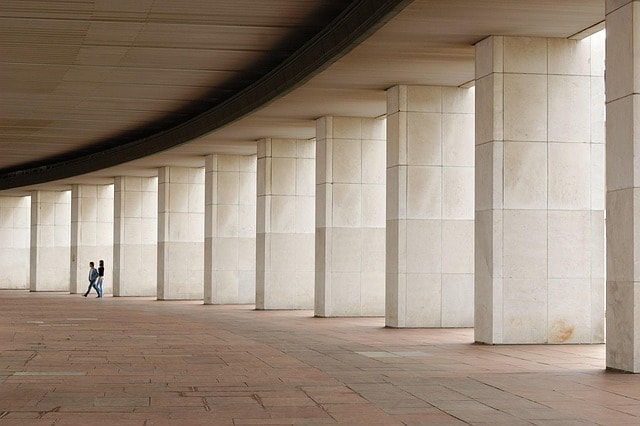
Inadequate mixing can create weak spots, increasing the risk of cracking and structural failure. Hand mixing is challenging for consistent quality due to inherent manual process variability. This inconsistency is why hand mixing is discouraged for critical structural elements like columns and shear walls. Beginners often add too much water, severely affecting the concrete’s strength and durability.
The mix ratio directly influences concrete’s workability and strength. Sea water in concrete mixing is discouraged due to potential corrosion and structural weakening. High permeability can cause issues like corrosion and reduced durability.
Vibration can improve a dry mix by liquefying it and releasing trapped air.
Dry Concrete Mix Problems
A dry mix shows difficulty in achieving necessary consistency and has a crumbly texture. When the concrete mix appears too dry, project outcomes can be negatively impacted, leading to diminished workability and reduced strength. The right consistency is crucial for strength and durability in finished projects.
To correct a dry mix, gradually add water while mixing to achieve the desired consistency. Add water slowly and incrementally to make the mix workable without becoming too wet. This approach maintains the concrete’s integrity and strength.
Runny Concrete Mix Issues
A runny mixture may result from incorrect water ratios and can be adjusted by reducing water content. Runny concrete often results from adding too much water during mixing. Excess water weakens concrete and prolongs setting time.
To correct a runny mixture, add small amounts of dry mix to achieve the desired consistency. If too wet, decrease water content or add more dry mix until the consistency is workable yet firm.
Ensuring correct ratios from the start prevents issues and results in quality concrete.
Cleaning Up After Mixing
Cleaning equipment after mixing prevents hardened concrete residue. Prompt cleaning prevents the formation of hard-to-remove concrete. Not cleaning a mixer may result in hardened concrete obstructing the paddles.
Cleaning tools after mixing maintains equipment efficiency and safety. Safety gear, including masks, protects against dust and chemical exposure during cleaning.
Choosing the Right Type of Concrete Mix
Different concrete mixes, such as nominal, standard, and design, serve varying construction needs based on ingredient proportions. Bagged concrete mix is convenient for small jobs. It is also the least expensive choice available. When selecting a concrete mix, use as little water as possible to achieve the best results.
Custom concrete mixes are formulated to meet unique project requirements and can include special additives for enhanced properties. Fiber reinforced crack-resistant concrete mix offers greater resistance to shrinkage cracks and impact damage, making it suitable for walkways with steps or landings.
Factors such as setup speed, surface durability, and weight capacity should be considered when choosing concrete for a project.
Summary
In summary, proper concrete mixing is essential for achieving strong, durable, and long-lasting concrete structures. By understanding and applying the right mixing methods, using the correct tools, and maintaining the ideal mix ratio, you can ensure the success of your concrete project. Whether you’re using hand mixing, machine mixing, or ready mix concrete, following these guidelines will help you achieve the best results. Remember, the key to quality concrete lies in the details of the mixing process.
Contact our Auckland concrete team today.
Frequently Asked Questions
How to make concrete?
To make concrete, use a standard mix of 1 part cement, 2 parts sand, and 3 parts gravel, ensuring you maintain these ratios for optimal results. Properly measuring these materials is crucial for achieving a smooth and durable finish.
What is the mix ratio for concrete NZ?
For strong concrete in New Zealand, a common mix ratio is 5 parts aggregate to 1 part cement. This typically requires about 6 bags of 40kg cement per cubic meter of concrete.
How many 20kg bags of cement to a cubic metre of concrete?
You will need approximately 100 bags of 20kg cement to create one cubic metre of concrete. This ensures you have the right mix for optimal strength and durability.
What is the ratio for mixing concrete?
The typical ratio for mixing concrete is 1 part cement, 2 parts sand, and 4 parts aggregates, which is a standard guideline for achieving a good strength. Alternatively, for a simpler mix, you can use a 3:2:1 ratio of blue metal, sand, and cement, which is also effective for most applications.
What is the importance of proper concrete mixing?
Proper concrete mixing is essential for maximizing strength and durability, which directly impacts the structural integrity and longevity of your project. Investing attention to this detail ensures a reliable and lasting outcome.
About the Author:
Mike Veail is a recognized digital marketing expert with over 6 years of experience in helping tradespeople and small businesses thrive online. A former quantity surveyor, Mike combines deep industry knowledge with hands-on expertise in SEO and Google Ads. His marketing strategies are tailored to the specific needs of the trades sector, helping businesses increase visibility and generate more leads through proven, ethical methods.
Mike has successfully partnered with numerous companies, establishing a track record of delivering measurable results. His work has been featured across various platforms that showcase his expertise in lead generation and online marketing for the trades sector.
Learn more about Mike's experience and services at https://theleadguy.online or follow him on social media: